
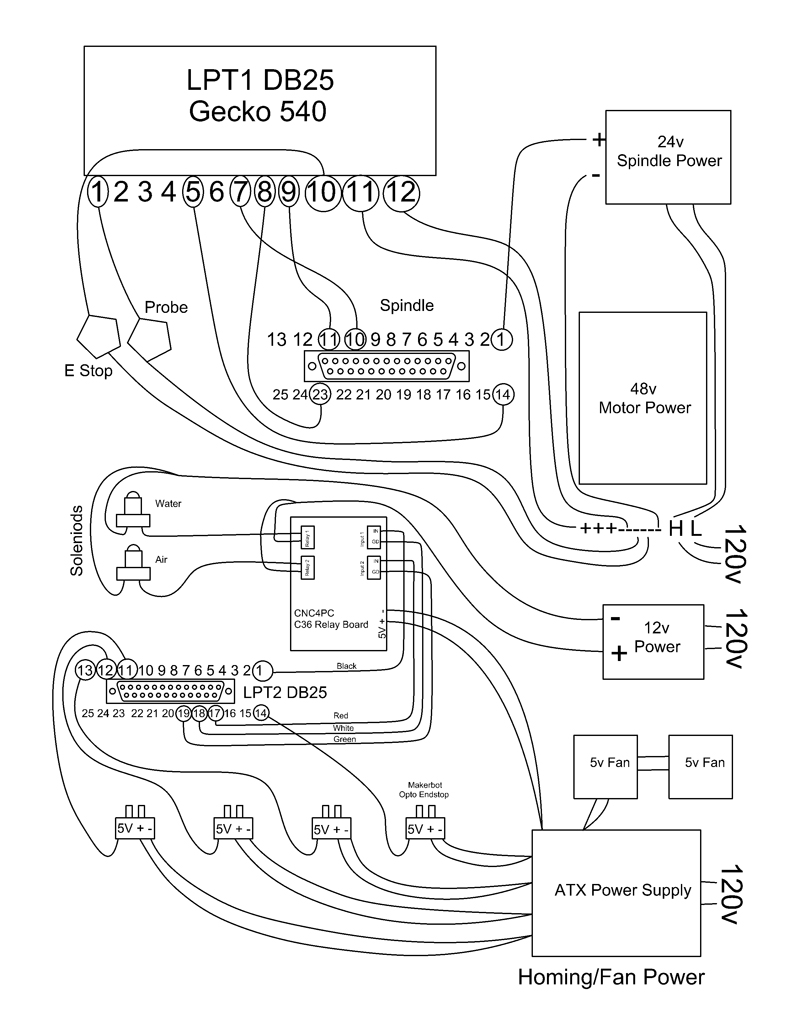
- #Gecko g540 wiring diagram for free
- #Gecko g540 wiring diagram drivers
- #Gecko g540 wiring diagram driver
Note that I use the ‘A-Axis’ to drive the second Y-axis Stepper so all steppers receive full current. I aimed for 2A and haven’t had any issues at all in the 2-3 years running. Basically solder up as per the drawing, put your multimeter on and turn the trimpot until your resistance is correct for the desired Amperage.
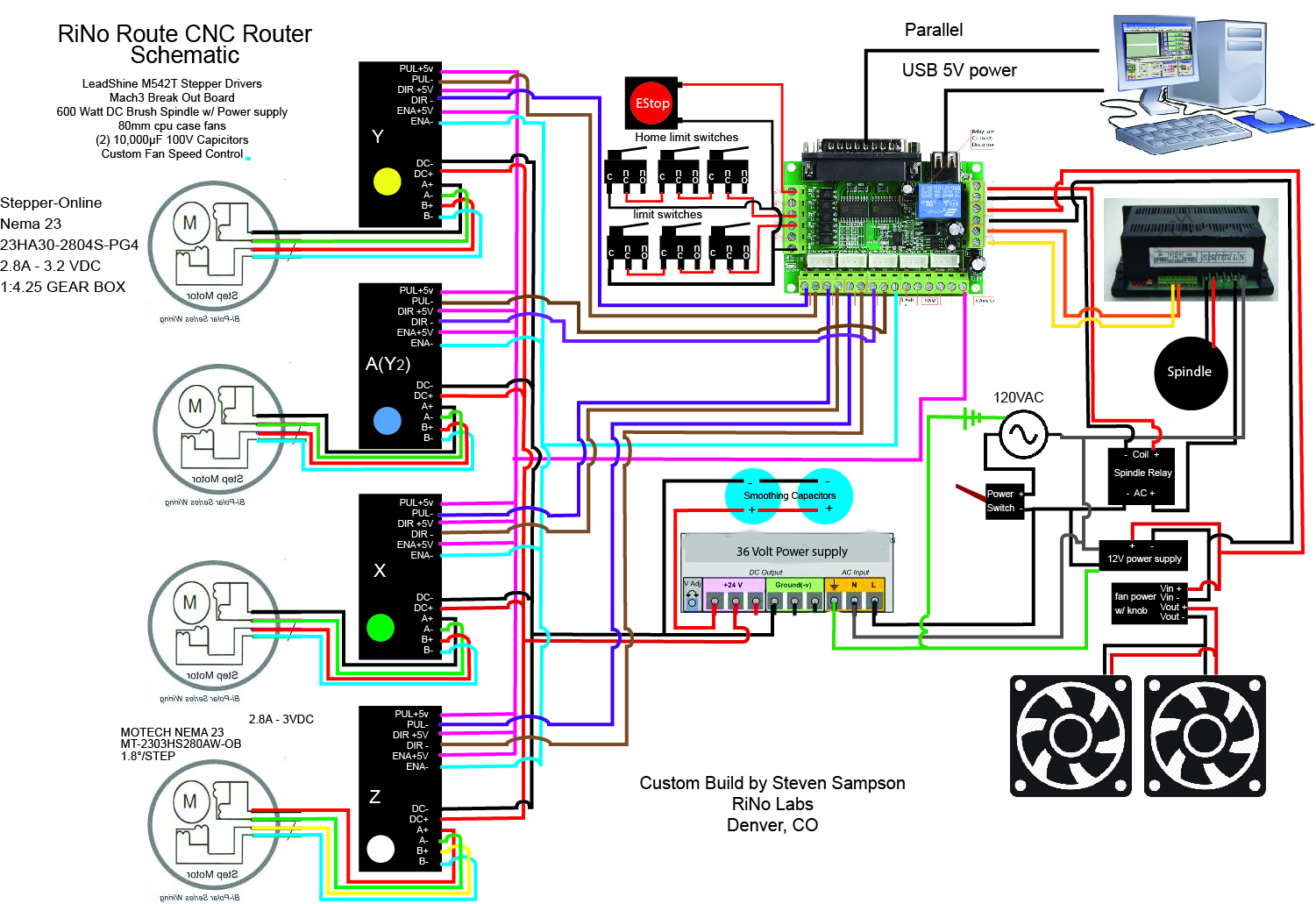
I definitely recommend these breakout boards, they made setting up the steppers so easy! To work out the coils, just touch any 2 of the four wires together, when the stepper gets hard to turn then those two wires belong to the same coil. Steppers are stock Shapeoko3, but I replaced all stepper cabling with shielded cable, and soldered on the stepper breakout boards. The UC300 requires 5V power, I found an old laptop power brick that supplies 5V and 12V, which works great for the UC300 and my Prox switches. I’ll detail this a bit more because I think it’s an upgrade that relatively inexperienced people can do, whereas I wouldn’t recommend the LinuxCNC path to a newer CNC’er. I have just bought a CNCdrive UC300ETH-5LPT motion controller, and a UCCNC Licence.
#Gecko g540 wiring diagram for free
I still think LinuxCNC is incredible for free software, and offers a lot, I just wanted something easier to get working the way I wanted. the bitsetter workflow) to work properly. It was super reliable and I ran it quite happily for a couple of years, but could never get probing or tool changes (i.e. I found LinuxCNC quite easy to run the machine, but initial setup was really hard for me to get my head around, I basically copied other people’s setups and changed bits and pieces to suit my hardware. I got the XXL running well under LinuxCNC, I extended the stepper and prox switch cables so I could have the control box separate to the CNC.
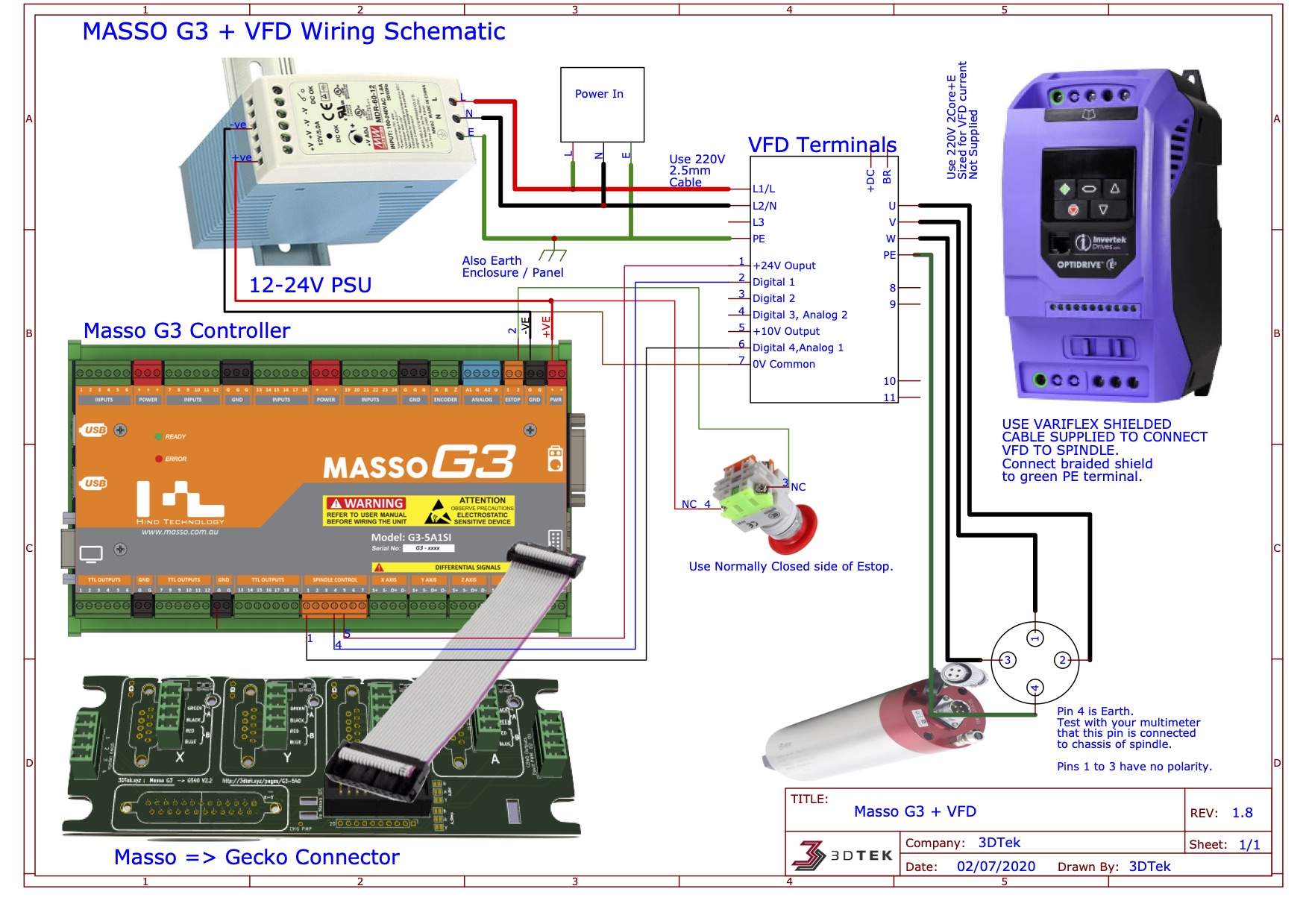
The Mesa 5i25 (not required for UCCNC option described below)
#Gecko g540 wiring diagram driver
The G540 Kit including 7.3A 48Vpower supply, E-stop, relay, power socketsĤx breakout boards to set driver current to Steppers In hindsight the G540 is perfectly capable for the Shapeoko, there was no need for the 5i25. The Mesa 5i25 is a motion control card that allows ‘realtime’ control, meaning zero lag at incredibly high feedrates and step frequencies. The G540 is basically a parallel port breakout board with 4x 3.5A drivers, but in a small robust package. I decided to try LinuxCNC because it’s free and incredibly powerful.
#Gecko g540 wiring diagram drivers
I didn’t have a huge amount of knowledge of drivers and software but my research got me to buying a Gecko G540 kit from an Australian distributer, and a Mesa 5i25 PCI-E card. I made the decision to upgrade the control system. During this time the XXL was released so I sold the original SO3 and bought the XXL – the intermittent disconnects were still an issue C3D were great, sending me new revisions of the (at the time very new) control board, new cables, and many other suggestions that improved the situation, but didn’t complexly resolve the issue. So my story starts with one of the very early Shapeoko 3s, and due to the old, poorly maintained electrical circuit in the rental house I was living in I had a huge amount of issues with disconnects.
